When it comes to manufacturing, waste isn't just about scraps on the floor. It's a whole host of things that drain your resources and time without adding any value. Sounds frustrating, right? Well, there's good news! The lean manufacturing approach identifies seven key types of waste, giving you a framework to tackle these productivity plagues head-on.
These wastes are more than just inefficiencies—they're opportunities for improvement. By zeroing in on these areas, startups can transform their operations into lean, mean, productivity machines. It's not just about cutting costs; it's about refining your process to get the best possible outcomes with the least effort.
Whether you're producing widgets or high-tech gadgets, understanding these wastes is crucial. You're not just reducing excess; you're paving the way for innovation and growth by clarifying processes and improving efficiency. Ready to learn more? Let's dig deeper into these seven wastes and figure out how to start scrapping them from your daily operations.
- The Concept of Waste in Manufacturing
- Overview of the Seven Wastes
- Tips to Reduce Overproduction
- Strategies to Minimize Waiting
- Streamlining Transportation in Manufacturing
The Concept of Waste in Manufacturing
In the world of manufacturing, the term 'waste' extends beyond just the leftovers on the production line. It's about any activity that consumes resources but doesn't create value for the customer. Sounds simple, right? But in reality, spotting these wastes can be quite tricky, leading to inefficiencies and lost profits.
Industries began realizing that much of their time and resources weren't going towards creating a final product that customers want. This is where the principle of lean manufacturing comes into play. It's all about maximizing value by minimizing waste, making sure that every step in the production process is worth it.
The Seven Wastes
There are seven kinds of waste that have been identified in the manufacturing realm. They include:
- Overproduction
- Waiting
- Transportation
- Inappropriate Processing
- Excess Inventory
- Unnecessary Motion
- Defects
By targeting these specific areas, companies can streamline their processes and save both time and money. For instance, overproduction waste happens when you make more product than what's needed, tying up resources that could be better used elsewhere.
Impact of Wastes
The impact of these wastes can be staggering. Analysts have noted that companies that successfully implement lean manufacturing techniques can boost productivity by 40-50%. This often results in significant cost savings, increased efficiency, and happier customers. It's not about working harder—it's about working smarter.
If you're looking to rethink your manufacturing setup or just get started the right way, analyzing and understanding these wastes is crucial. Trust me, recognizing these can set you on a path of sustainable growth and operation excellence.
Thinking about it this way, managing waste is like decluttering a messy room. It feels daunting at first, but once you start, everything else just falls into place, revealing a streamlined and efficient environment. And that, my friend, is the beauty of lean manufacturing.
Overview of the Seven Wastes
Welcome to the world of lean manufacturing—where the focus is on trimming the fat to make things run smoother and faster. The seven wastes we're tackling are like the seven deadly sins of the industrial world. They're sneaky and can creep in anytime, slowing things down and causing headaches.
First up is overproduction. Making more than you need sounds harmless, but it ties up your cash in unnecessary stock and increases storage costs. A cool tip here? Produce based on actual demand to keep things lean.
Then, there's waiting. Idle time equals money lost. Think of it as your factory twiddling its thumbs, whether that's waiting for materials, equipment repairs, or information. Keeping processes flowing smoothly can help cut down the waiting game.
Next, transportation waste. It’s basically unnecessary movement of products. Each time a product is moved, there's potential for damage and delays. Streamlining your transport routes and cutting down on unnecessary trips are great ways to tackle this waste.
Extra Processing
Then there's extra processing. Doing more work than needed isn’t just tiring, it's wasteful. Focus on providing what's needed—no more, no less—by setting clear specifications and sticking to them.
Let’s not forget inventory. Stacks of unsold product or excess raw materials gathering dust don't do anyone any favors, right? Keep inventory levels optimal to balance supply with demand while avoiding costly overstock.
Motion Waste
We also have motion waste. This isn't about transportation—it's the unnecessary movement of people or equipment. Ergonomics and efficient layouts can slash this waste, keeping everyone safer and more efficient.
Finally, there's defects. Mistakes or faulty products can cause a heap of trouble. Investing in quality control upfront can save hassle down the line by catching issues early before they balloon into bigger problems.
Seeing these seven wastes in action clarifies how they can bog down a system. Addressing them systematically isn't just smart—it's essential for thriving in today's competitive manufacturing world.
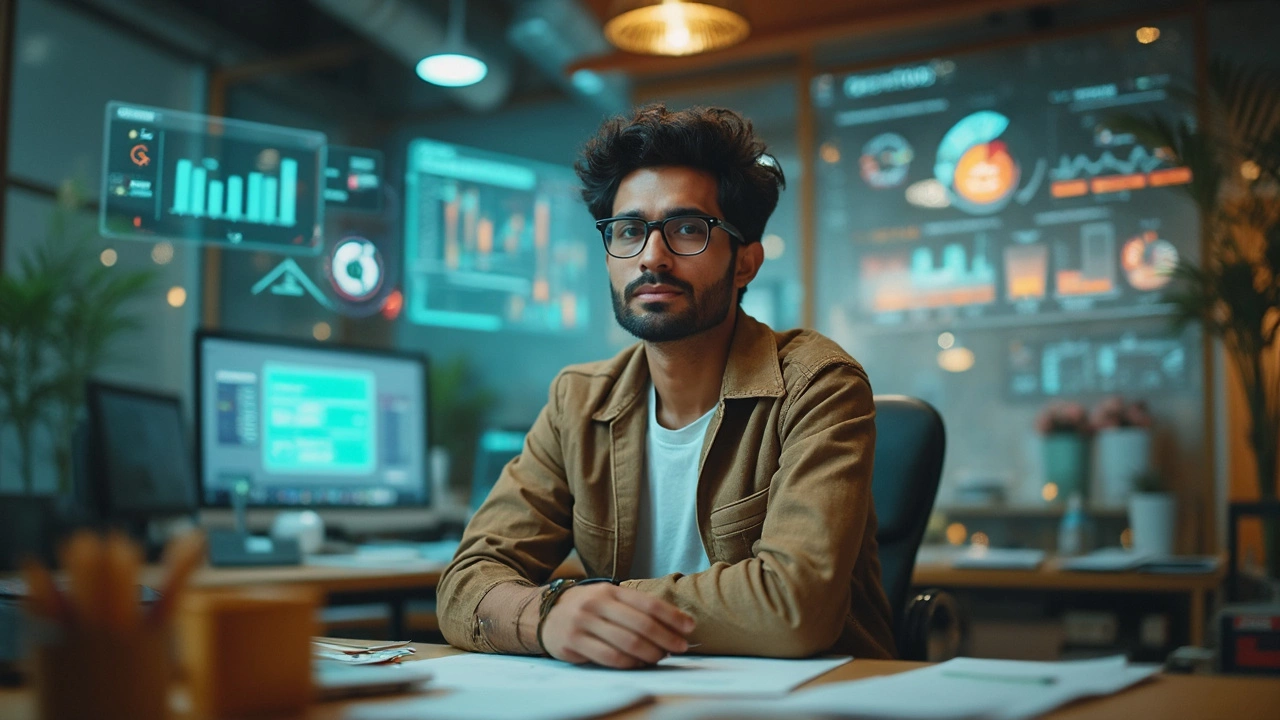
Tips to Reduce Overproduction
Overproduction in manufacturing is like filling your plate with more food than you can eat—it sounds like a good idea at first but often leads to waste. Manufacturing waste in the form of overproduction doesn't just deplete resources; it clogs up storage, complicates distribution, and can shrink your profits.
Take Advantage of Demand Forecasting
One of the first steps to tackle overproduction is getting a handle on demand. Use modern tech tools and data analytics to forecast your product needs. Many software solutions provide predictive analytics that help adjust your production scale in real time. This means less guesswork and better alignment with actual market demand.
Adopt Just-In-Time Production
The lean manufacturing principle of Just-In-Time (JIT) is all about producing what you need when you need it. It requires a tight collaboration with your suppliers and a keen eye on inventory levels. This method reduces the likelihood of overproduction while keeping everything streamlined and efficient.
Implement a Pull System
Unlike a push system, which pushes products ahead whether they're needed or not, a pull system uses real customer demand to dictate production. This ensures you're only making products as fast as they're being ordered, keeping excess stock from piling up.
Ensure Efficient Inventory Management
Good inventory management is key. Regularly audit your stock to identify slow-moving items that may lead to overproduction. Smart inventory software can automate this process and help you keep track of stocks efficiently, so you know exactly what's needed and by when.
Consider Smaller Batch Sizes
Producing in smaller batches allows for greater flexibility and responsiveness to market demands. It might seem counterintuitive, but small changes can yield significant results. Smaller batches mean less commitment to potentially unsellable stock and more adaptability to trends.
Tackling overproduction involves a combination of strategies. By focusing on demand, keeping inventory tight, and producing only what you need, you can slash manufacturing waste and boost efficiency—turning a once tangled process into a streamlined operation geared for success.
Strategies to Minimize Waiting
Waiting is a sneaky waste in the world of manufacturing waste. It's that idle time when nothing's moving forward, and it's not just annoying—it costs money. How do you kick it to the curb? Let's check out some practical ways to get things flowing.
Streamlined Communication
One of the biggest causes of waiting in a manufacturing setup is miscommunication. Tightening up communication between management, teams, and machines can work wonders. Using tools like Slack for real-time updates or implementing a simple signaling system can cut down on those 'Who’s doing what?' moments.
Improved Scheduling
Ever heard the saying, "Time lost is never found again"? Proper scheduling ensures everything and everyone’s ready when needed. An effective way is to use project management software that keeps everyone on the same page about timelines and processes. Kanban boards can be a lifesaver when you’re juggling multiple tasks.
“Time is really the only capital that any human being has, and the only thing he can't afford to lose." – Thomas Edison
Maintenance Routine
Waiting isn’t just about people; machines can cause hold-ups too. Regular maintenance keeps equipment in top shape and reduces downtime. Set up a calendar reminder to check machinery. This simple step can prevent those frustrating delays when a line suddenly stops.
Automation and Technology
If you’re not using smart tech solutions, you might be doing yourself a disservice. Simple automation tools help in reducing repetitive tasks, which in turn minimizes waiting time. Even investing in a basic workflow automation tool can make operations smoother and faster.
- Manufacturing waste like waiting is often addressed by redesigning the layout of processes to eliminate delays.
- Implementing lean manufacturing methods can reduce cycle times by up to 40%.
Minimizing waiting might take some effort initially, but the payoff is substantial. Once you make these changes, the smoothness of operations and the free flow of work can be a game-changer. No more twiddling thumbs—just productive, efficient workdays.
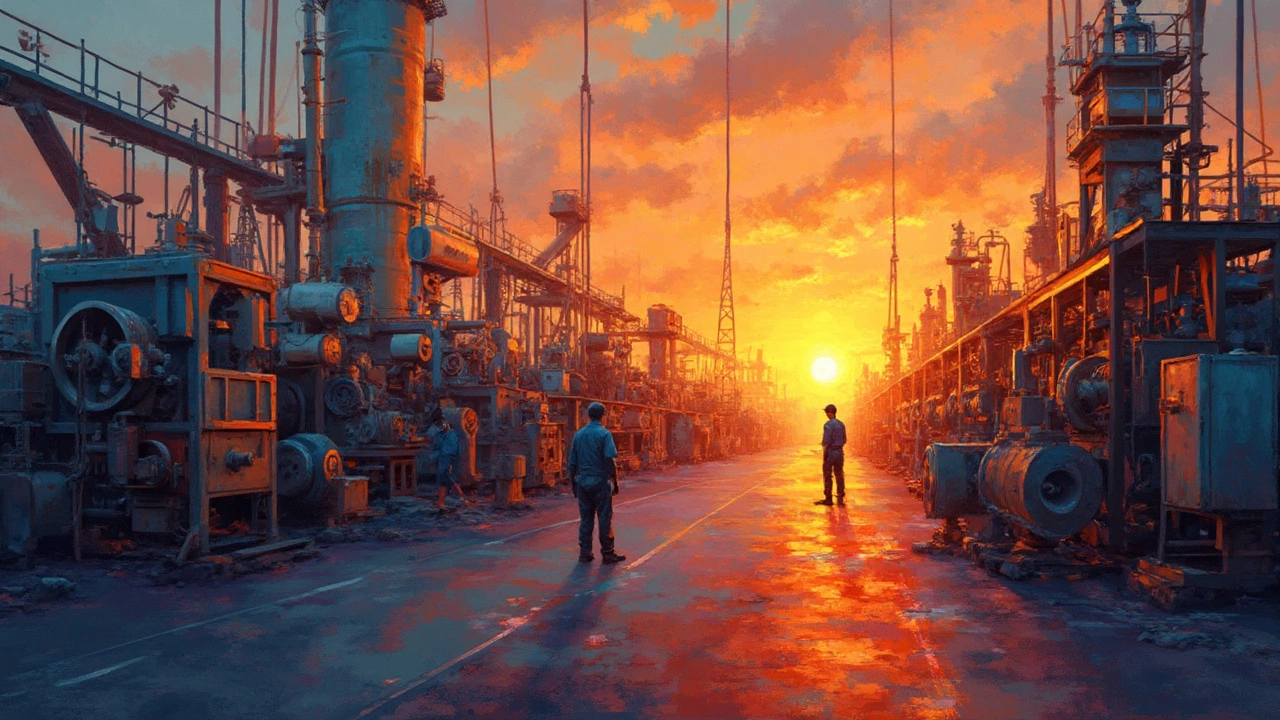
Streamlining Transportation in Manufacturing
Transportation in manufacturing isn't about trucks and roads—it's about how materials and products move through your factory. Unnecessary movement can slow you down more than you'd think. Reducing this waste can cut costs and boost efficiency, so let's dive into how to make your transportation leaner.
Identify Bottlenecks
First off, know where things are slowing down. Is there a spot where materials pile up or production halts because someone has to fetch extra parts? Those are clues. A little detective work can help you spot bottlenecks, and fixing them can make a huge difference.
Optimize Layout
Once you've pinpointed the choke points, look at your layout. Could moving a machine or workstation trim down some unnecessary steps? Streamlining the plant floor is a classic lean manufacturing strategy that puts everything in the right place to keep things flowing smoothly.
Invest in Efficient Equipment
Sometimes the problem might be the equipment itself. Old or slow gear can create delays you don't need. It might be worth investing in newer, faster tech to keep things moving. Sure, it has a cost, but it often pays off in the long run with more efficient production.
Embrace Automation
Automation isn't just for big players anymore. Even smaller startups can find ways to use smart technologies to move materials without lifting a finger. Automated guided vehicles (AGVs) and conveyor belts can help reduce wasted movement and free up your team for tasks that need a human touch.
Monitor and Adjust
Nailing down transportation waste isn't a one-time task. Keep an eye on your processes and be ready to tweak as needed. Regular check-ins and data analysis can alert you to new inefficiencies, so you're prepared to tackle them before they become real headaches.
If you're convinced that trimming transportation waste sounds like the way to go, then you're on the right track. Making these changes can feel daunting, but incremental steps can lead to significant improvements.
Year | Reduction in Transportation Waste (%) |
---|---|
2023 | 8% |
2024 | 12% |
2025 | 15% |
This kind of progress isn’t just about efficiency; it’s about getting ahead of the game in a competitive market. So, gear up and start streamlining!
Write a comment