In the world of commerce and industry, manufacturing often takes center stage. It's the pulse that keeps economies alive, turning raw materials into products that reach homes and businesses around the globe. Yet, this essential sector isn't without its hurdles. Challenges of various scales loom large, impacting everything from economic stability to environmental sustainability.
Diving into the issues of manufacturing reveals a complex web of problems that demand attention. From economic downturns and shifts in consumer demand to the push for sustainable practices, these challenges require innovative solutions. Governments around the world recognize this, rolling out schemes and initiatives designed to support and transform the industry. Let's explore what these challenges entail and how government interventions could pave the way for progress in manufacturing.
- Current Challenges in Manufacturing
- Economic Impacts and Trends
- Environmental Considerations
- Technological Innovations and Limitations
- Government Interventions and Support
Current Challenges in Manufacturing
Manufacturing, often heralded as the backbone of economic development, faces a series of significant challenges today. These hurdles are as varied as they are complex, encompassing economic, regulatory, technological, and environmental dimensions. The rise in raw material costs has posed a serious threat to profitability for manufacturers across the globe. Price volatility, driven by geopolitical tensions, trade wars, and the recent disruptions in global supply chains, means manufacturers have to constantly adjust their operations in response to fluctuating input costs. A stark reminder of this came during the COVID-19 pandemic, where swift shifts in demand and supply chain disruptions caught many unprepared, underscoring the need for resilience in manufacturing processes.
Adding to the economic strains are labor challenges. Many manufacturing sectors face a significant skills gap, where the workforce lacks the expertise needed for high-tech industries. As automation and digitalization advance, the demand for skilled workers who can operate and maintain modern machinery is increasing. Yet, educational and training institutions are struggling to keep pace with evolving industry requirements. According to a recent report by the World Economic Forum, the sector could face a shortage of over 10 million skilled workers by 2030 if current trends continue.
Technological integration presents yet another challenge. While it's true that technology enhances efficiency, governance over this transition can be cumbersome. Some manufacturers remain hesitant about investing in new technologies due to high initial costs and uncertain returns. A research study carried out by McKinsey & Company found that more than 70% of manufacturing firms plan to integrate more automation and artificial intelligence into their processes. However, many remain in the early stages of adoption, stymied by the complexity and expense involved.
Environmental considerations also weigh heavily on manufacturers. With global emphasis now shifting toward sustainability, industries face mounting pressure to reduce their carbon footprints and embrace eco-friendly practices. This means rethinking processes, materials, and designs to align with environmental standards. Compliance with increasingly stringent regulations demands a level of innovation and investment that not all manufacturers can afford. The International Energy Agency has reported that the industry sector accounts for more than 25% of global emissions, underscoring the necessity for change.
Finally, geopolitical and regulatory changes cannot be ignored. As new trade policies emerge and political landscapes shift, manufacturers must navigate an often-unpredictable regulatory environment. These challenges are magnified for those with global supply chains stretching across multiple jurisdictions, each with its compliance requirements. This fluid landscape makes strategic planning difficult, as decisions must often be revisited and revised in light of new policies.
"As we face an unprecedented pace of change in manufacturing, our ability to adapt and innovate becomes our most important strategic asset," notes Mary Barra, CEO of General Motors.
In essence, the challenges in manufacturing are multi-faceted, requiring a blend of flexibility, foresight, and innovation to address effectively. As the sector evolves, so too must the strategies employed by those steering its course, balancing immediate needs with long-term sustainability and success.
Economic Impacts and Trends
In the realm of manufacturing, the economic impacts can be both profound and far-reaching. This sector does not exist in isolation; it's intricately linked to the performance of both local and global economies. Manufacturing drives economic growth by creating jobs, boosting exports, and fostering innovation. However, it is also a sector susceptible to economic fluctuations, reflective of broader market trends and geopolitical shifts. When global demand for goods ebbs, it often results in production slowdowns, affecting employment and investment. Supply chain disruptions, like those experienced during recent global events, have spotlighted vulnerabilities within the system and highlighted the fragility of dependent economies.
The trends within this sector also evolve at a rapid pace. A significant trend that has taken hold is the shift towards automation and the integration of smart technology. While these advancements promise increased efficiency and productivity, they also pose economic challenges, such as job displacement and the need for workforce reskilling. The global nature of supply chains means that a small disruption in one part of the world can have domino effects, impacting economies thousands of miles away. Amidst these changes, many countries have been actively seeking ways to bolster their manufacturing base through strategic investments and policy reforms.
According to a recent report by the World Economic Forum, "The future of manufacturing is not about making more products faster, but about making smarter, more efficient processes."
Various economic policies are also in play to stimulate the manufacturing industry. Governments are offering incentives to companies investing in new technologies and sustainability practices. These include tax breaks, grants, and subsidies designed to encourage local production and reduce dependency on imports. Additionally, trade agreements are being renegotiated to ensure fairer market access and competitive pricing, keeping domestic industries viable and competitive. Observing market movements, a recurring theme emerges: the need for adaptability in face of ever-changing demands and conditions.
Analyzing data trends reveals some intriguing insights into the future of manufacturing. For instance, emerging markets are becoming powerhouses, increasing their share of global manufacturing output. Companies are prompted to reconsider their strategies, deciding whether to nearshore or offshore their operations based on cost-effectiveness and market access considerations. Envisioning the economic landscape of tomorrow involves not just understanding current impacts but anticipating future challenges and seizing opportunities for growth. As the dynamics of global manufacturing continue to evolve, staying informed and adaptable will be key players in ensuring sustained economic success.
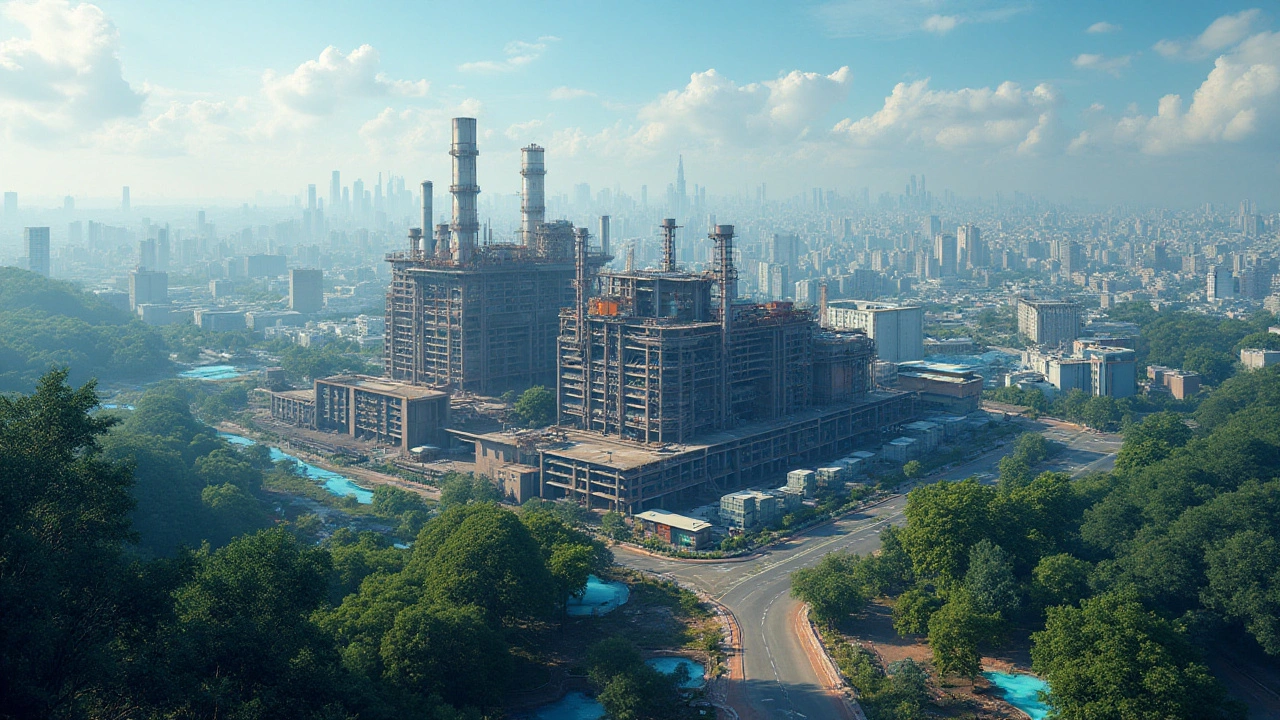
Environmental Considerations
The manufacturing industry is undeniably crucial to our day-to-day lives, yet it comes with its own set of environmental challenges that can't be ignored. The **manufacturing** process, from raw material extraction to product delivery, often involves significant energy consumption and emissions. This not only impacts our natural ecosystems but also contributes to climate change, which has become a pressing global concern. Addressing these environmental considerations requires a multifaceted approach that balances industrial growth with sustainable practices.
One prominent area of concern is the carbon footprint associated with traditional **manufacturing** methods. Factories often rely on fossil fuels, which are an abundant source of energy but also a major contributor to greenhouse gas emissions. Reducing these emissions requires innovative solutions such as adopting renewable energy sources or investing in energy-efficient technologies. In fact, a study by the International Energy Agency (IEA) highlights that the industrial sector accounts for more than 30% of global energy demand. This staggering statistic underscores the critical need for change.
Another significant aspect involves waste management within the **manufacturing** sector. The process generates substantial quantities of waste, including solid waste, chemical by-products, and wastewater. Properly managing this waste is crucial to minimize its harmful impact on the environment. Fortunately, many companies are now implementing circular economy principles, which emphasize reducing waste through recycling and reusing materials. These efforts align with global environmental goals and help diminish the strain imposed on our planet.
Noise pollution is yet another critical environmental concern linked to modern **manufacturing** facilities. The machinery and equipment used in these plants often produce significant levels of noise, affecting local wildlife and disrupting human communities. Implementing noise reduction technologies and proper zoning regulations can mitigate these issues, ensuring that factory operations don't detrimentally impact surrounding areas.
The role of policy and regulation in navigating environmental challenges cannot be overstated. Governments worldwide are creating frameworks that encourage sustainable practices within the **manufacturing** arena. This often involves offering incentives for companies that adopt cleaner technologies and penalizing those that fail to comply with environmental standards. In some regions, governments are setting ambitious goals for reducing carbon emissions and implementing stricter guidelines on waste disposal.
"It is in our collective interest to ensure that environmental considerations are at the forefront of our manufacturing processes," says Dr. Emma Wilson, an environmental policy expert. "Responsible manufacturing practices not only benefit the environment but also create new opportunities for innovation and efficiency."
Technological Innovations and Limitations
In the rapidly evolving landscape of manufacturing, technology stands as both a catalyst for progress and a barrier. On one hand, innovation in automation, robotics, and artificial intelligence has propelled the manufacturing sector to new heights, offering unprecedented efficiency and precision. Automation streamlines production lines, reducing human error and labor costs, thereby boosting productivity and output quality. Robotics, for instance, are increasingly employed in assembly lines for tasks ranging from intricate component assembly to packaging, enabling a speed and accuracy that humans alone could scarcely achieve.
Despite these advances, technological limitations resist the full potential of innovation. One of the primary hurdles is the high initial investment required for the latest technology. Small and medium-sized enterprises, which form the backbone of many economies, often struggle to muster the resources needed for such large-scale upgrades. This financial barrier limits the equitable distribution of technological benefits across the industry. Moreover, the integration of new tech requires not just monetary investment but also a skilled workforce adept at operating and maintaining these advanced systems. The digital skills gap looms large, with many workers still unprepared to adapt to high-tech environments.
Interestingly, the rapid pace of change can be both a boon and a bane. What was cutting-edge a year ago might today be obsolete, pressuring businesses to keep constantly updating. Quote from a leading industrial expert, "Technology in manufacturing is like a double-edged sword; it drives us forward, yet we must tread carefully to not cut ourselves with its double cost and constant demands." Moreover, there are challenges related to cybersecurity as more systems become digitized. The risk of industrial espionage and data breaches underscores the need for robust cyber protections, which can stretch company budgets further.
The environmental impact of technological applications in manufacturing cannot be ignored. While technology offers cleaner production processes and waste reduction tactics, the energy consumption of high-tech machines contributes to the industry's carbon footprint. Balancing innovation with sustainability is a complex dance requiring concerted efforts and creative solutions. A 2023 study highlighted that despite advancements, the manufacturing industry globally accounted for approximately 20% of greenhouse gas emissions.
Technological trends like the Internet of Things (IoT) and Industry 4.0 offer exciting prospects for interconnected manufacturing processes and real-time data collection, presenting both opportunity and challenge. Many companies are still in the nascent stages of IoT integration, facing difficulties in aligning their traditional processes with modern technologies. As 2025 unfolds, how manufacturing navigates these technological waters will significantly impact its development and the broader economy.
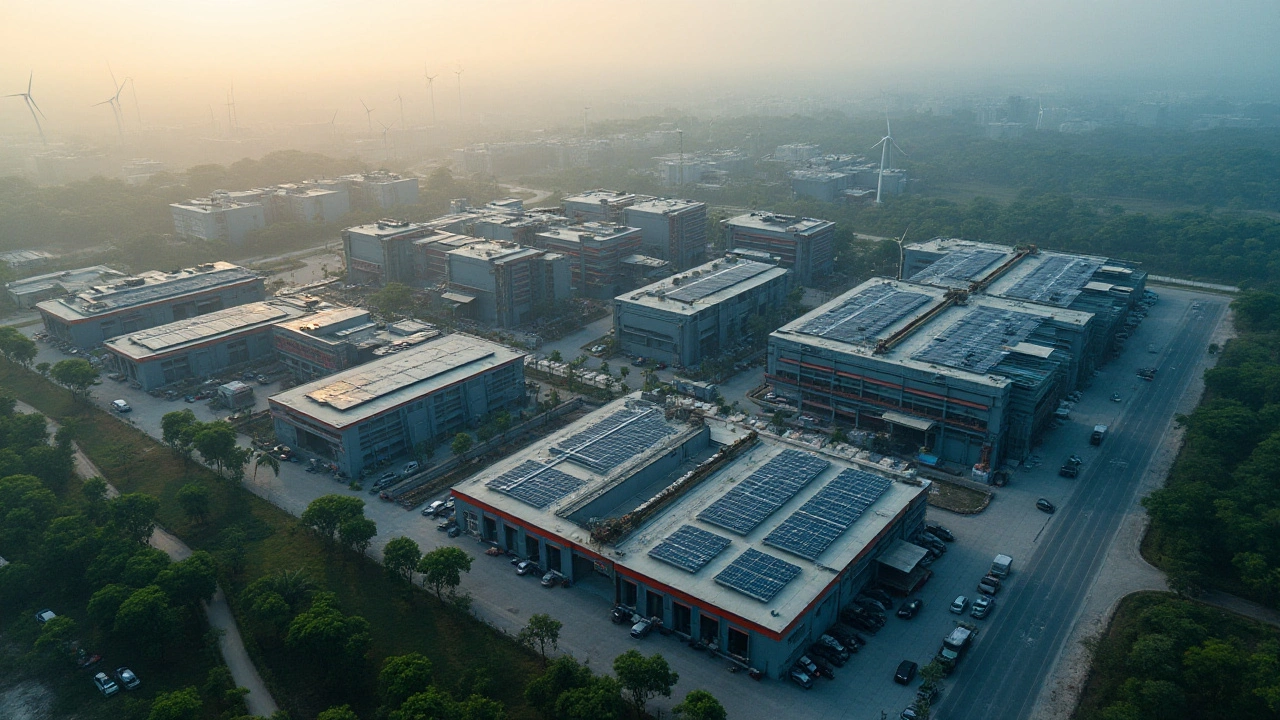
Government Interventions and Support
The manufacturing sector's challenges are multifaceted, and governments around the globe have recognized the necessity of stepping in and providing comprehensive support to bolster this critical industry. With changing times, there's been a shift in how industrial policies are formed—focusing more on long-term sustainability rather than merely short-term gains. Developed and developing nations alike are formulating strategic interventions aimed at resolving the core issues that plague manufacturing. The role of government has evolved from a mere regulatory authority to an active player in fostering growth and innovation, addressing the sector's woes through targeted schemes and policies.
One of the key strategies involves direct financial subsidies and tax incentives for manufacturing companies. This approach boosts competitiveness and invites investment. For instance, in the European Union, the Horizon 2020 initiative has allocated extensive funding to support research and innovations within the manufacturing sectors. By providing financial backing, governments are equipping companies with the necessary resources to advance their capabilities and explore new markets. Another noteworthy initiative is the 'Make in India' campaign, aimed at transforming India into a global manufacturing hub by simplifying processes, enhancing infrastructure, and promoting investments from international ventures.
Besides monetary incentives, there's a growing emphasis on technology adoption and innovation as a part of these interventions. Digital transformation schemes encourage manufacturers to integrate advanced technologies like AI, IoT, and robotics into their operations. The Industry 4.0 trend is a testament to these efforts, as it beckons a new era of automated manufacturing practices. Several countries have launched digital acceleration programs that provide the technical training and infrastructure needed to implement such technological advancements, helping industries transition smoothly into this new age.
Environmental sustainability plays a pivotal role in many government schemes. With an increasing focus on eco-friendly practices, schemes such as carbon credits and mandatory compliance with environmental standards encourage manufacturers to adopt greener methods. The NZ Government's Emissions Trading Scheme is a step towards encouraging industries to reduce their carbon footprint, aligning with the country's broader goals of achieving net-zero emissions. By weaving environmental considerations into these programs, governments not only tackle manufacturing inefficiencies but also contribute to vital global sustainability efforts.
"Manufacturing is a driver of growth and development and represents a core pillar of economic resilience. Governments must approach the solution to its challenges with both resolve and innovation," said Margareta Drzeniek-Hanouz, Head of Economic Growth Initiatives.
To further support manufacturing, vocational training programs and skill development workshops are being introduced. These initiatives aim to bridge the skill shortages prevalent in the industry today. By ensuring that the workforce is equipped with up-to-date skills, these programs enhance productivity and innovation, directly addressing one of the sector's longstanding challenges. Educational institutions are partnering with governments and industries to curate curriculums that align with current and future manufacturing trends, creating a robust pipeline of talent proficient in both traditional and cutting-edge skills.
The collaborative nature of these interventions indicates a departure from isolated policies towards holistic approaches. Governments engaging with industry leaders, researchers, and educational institutions create an ecosystem that nurtures growth. Emphasizing public-private partnerships unlocks new opportunities and pathways for transforming the manufacturing landscape. As these schemes evolve, they not only offer support but lay down the blueprint for a thriving, sustainable, and adaptive manufacturing sector that is primed for future challenges and opportunities.
Write a comment