Imagine factories grinding to a halt or construction sites standing quiet. Hard to picture in a country like the US, right? The lifeblood of all that energy—the machinery that keeps America moving—often doesn't even come from within its own borders.
The Big Players: Where US Machinery Comes From
Selecting a piece of imported machinery for an American business usually means reaching out to a handful of dominant countries. Year after year, US machinery imports lean heavily on just a few trusted trade partners. China, Germany, Japan, Mexico, and Canada are the heavy hitters here—providing everything from factory robots to farm equipment to the gear used in everything from airports to hospitals.
The numbers underline their clout. According to the latest US Census Bureau stats, for 2024, the US imported over $440 billion worth of machinery, not counting electrical gear (which is tallied separately). China led the pack, sending more than $85 billion in machinery. Germany followed with about $53 billion, Japan with roughly $32 billion, with Mexico and Canada both close behind—each contributing tens of billions to that tally.
These countries aren’t winning the market by accident. China pushes prices lower, supplying both generic options for budget buyers and quality brands for precision manufacturing. Germany brings its A-game: think advanced machine tools, automotive equipment, and robotics. The Japanese are still kings in automation and electronics-driven machinery, with brands like Fanuc or Komatsu recognized around the world. Mexico keeps shipping up affordable engines, pumps, heating, and cooling kits for everything from cars to home appliances. And Canada’s niche? Farm, mining, and energy-sector machinery made for tough conditions.
It’s not all about who’s cheapest or closest, though. American buyers also look at reliability, parts availability, safety standards, and after-sales service. Ever wonder why German CNC machines are so common in Midwest tool shops? That’s why. Even if they come with a bigger price tag up front, downtime can cost much more in the long run.
The product categories themselves are huge. They include industrial robots, computers for manufacturing, pumps and compressors, bulldozers, cranes, printing presses, even food processing gear. Whether you’re buying an MRI scanner for a new hospital wing or a row of seeders for an Iowa farm, odds are good that at least a part of it was stamped "Made in China," "Germany," or another familiar export powerhouse.
If you’re curious about what all this looks like in numbers, check out this quick overview of 2024’s leading suppliers:
Country | Machinery Imports to US (in $ billions, 2024) |
---|---|
China | 85.1 |
Germany | 53.2 |
Japan | 32.7 |
Mexico | 31.8 |
Canada | 26.3 |
If you look around any busy American port—say, the Port of LA or Savannah—crates marked from these countries fill the docks. But don’t think the list stops here: the US also brings in machinery from South Korea, Italy, the UK, Switzerland, and even Taiwan. Demand shifts quickly, especially as technologies evolve and supply chains adjust.
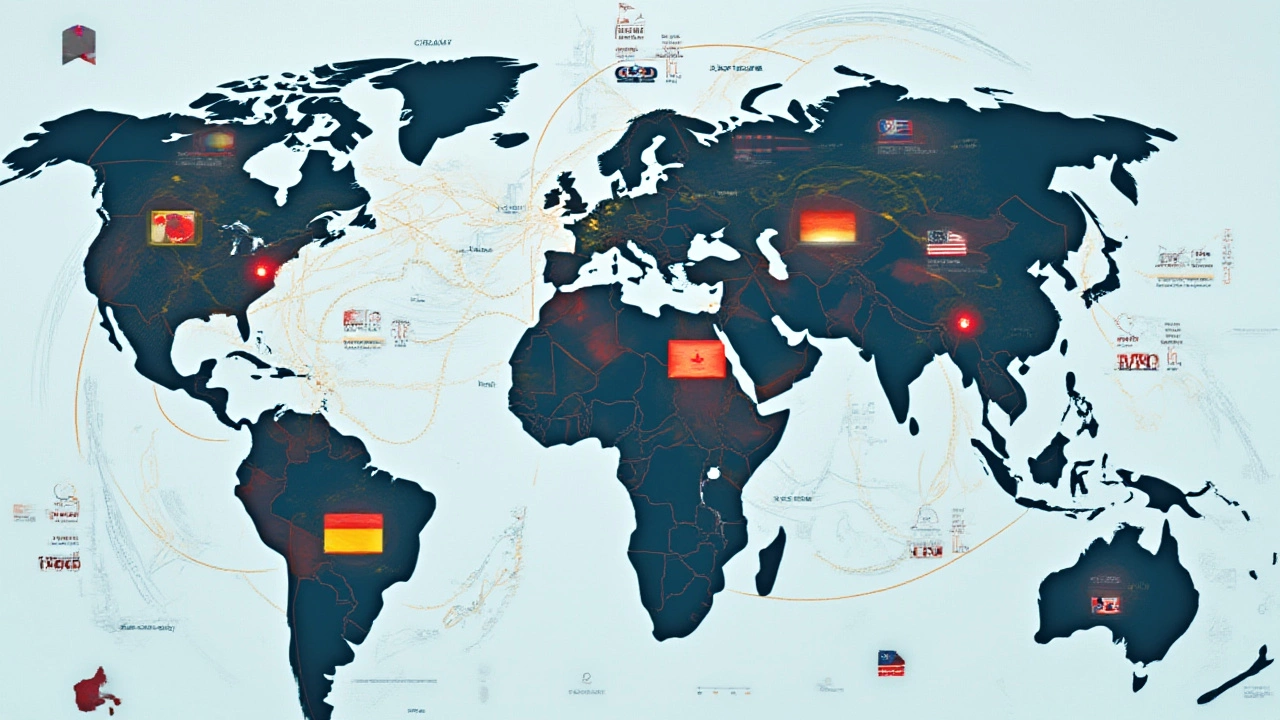
Why Machinery Imports Matter to the US Economy
This isn’t just an exercise in flag-spotting. Machinery imports are tightly woven into the US economy’s DNA. For manufacturing giants—whether churning out cars in Detroit or crafting microchips in Texas—dependable machinery is what keeps them ahead. And with American consumers and companies demanding the latest tech, sticking to only what’s built at home isn’t practical (or profitable).
Imports help fill the innovation gap. Many US companies simply don’t make certain kinds of machinery. For example, Japanese and German firms are years ahead on industrial robots and ultra-precise tools for delicate medical or semiconductor work. It’s faster and often cheaper to import these than to try to build up that tech base from scratch.
The US machinery market is also fiercely competitive. Domestic makers (like Caterpillar, John Deere, or Haas) thrive alongside imports, but often focus on their own specialties or compete by tailoring service, support, or custom solutions. The reality? Even US manufacturers sometimes rely on imported components to finish their products—think Japanese robotics arms in American-built assembly lines or German precision gears in locally made packaging machines. Most “US made” cars have some foreign machinery under the hood or shaping the steel.
Yet this reliance comes with trade-offs. When supply chains choke up—as the world saw during the COVID-19 pandemic—factories face delays, costs shoot up, and sometimes entire industries stutter. That’s sparked renewed interest in “reshoring,” or bringing more manufacturing back to the US, but progress here is steady and slow. The expertise, cost structure, and scale that China or Germany have built up can’t be copied overnight.
Trade agreements shape the flow, too. The USMCA (replacing NAFTA) means a lot of the machinery streaming in from Mexico and Canada enjoys tariff-free entry—boosting regional trade and helping American factories keep their supply chain headaches under control. In contrast, the US and China have spatted over tariffs since 2018, making some categories of Chinese machinery pricier or riskier for importers. Still, price tags and product availability keep China in the lead.
Some savvy American businesses hedge their bets by diversifying suppliers, buying gear from more than one country or keeping a blend of imported and US-made machinery on hand. It’s one way to keep operations running, even when geopolitical squabbles flare up or container ships stack up offshore.
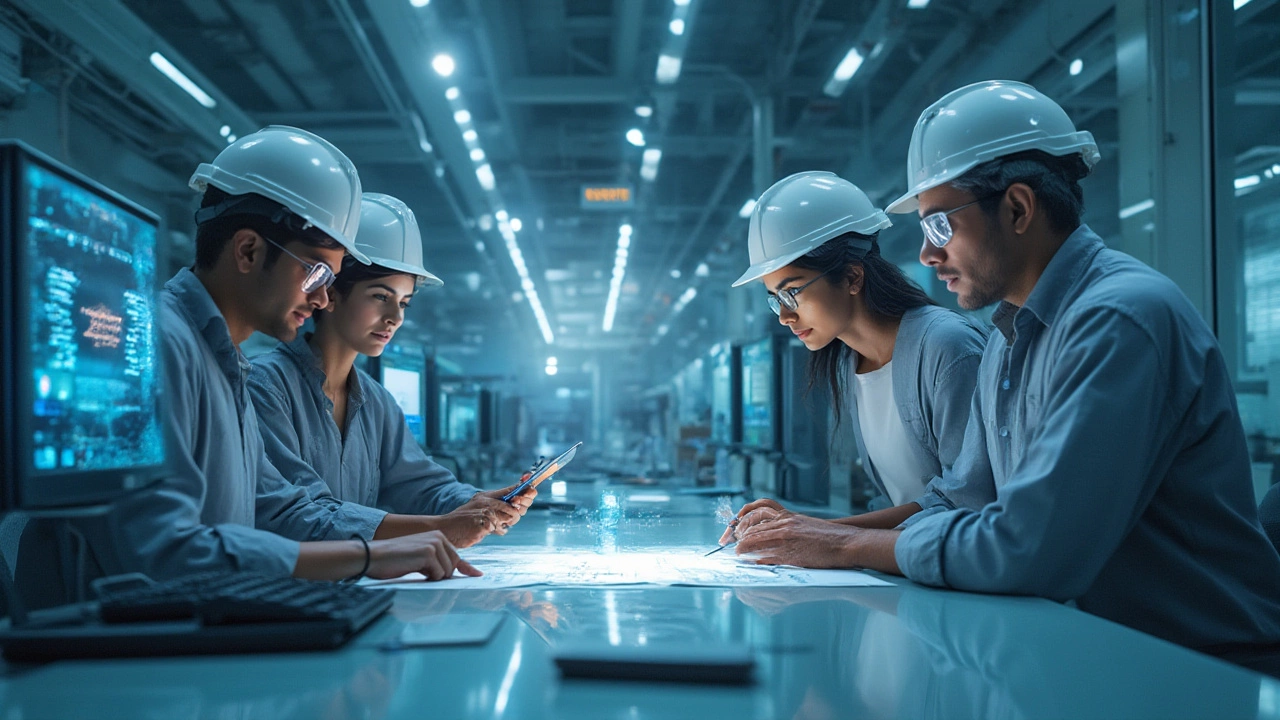
Getting the Edge: How Businesses Choose Machinery Imports
So, let’s say you’re running an American business and need a couple of new robotic arms for your factory line. Where do you even start?
First, it’s usually specs before stickers. Companies weigh things like performance, warranty, cost of ownership (not just the upfront price), spare parts, and how easily repairs can be handled. Japanese robotics firms like Yaskawa or Fanuc might win for accuracy and reliability, while a Chinese competitor offers a great deal but with less robust aftersales support.
Next up: compliance with US safety standards. Not every imported machine can get the green light from OSHA or the FDA. Smart buyers check certifications—UL, CE marks, and alike—or risk expensive delays when shipments get held up at customs or, worse, can’t be legally used stateside.
Another big factor is service. A German machine might be the gold standard, but if there’s no US-based technician, downtime can get costly. That’s why so many global giants now plant US service and distribution centers: it keeps their gear in the running for contracts, especially when round-the-clock use is on the line.
There’s also the question of financing and leasing. Importers sometimes offer rock-bottom deals, but with catch-22s—like tricky payment terms, higher insurance costs, or language barriers on manuals and support calls. Savvy buyers ask around, look up online reviews, and contact other customers. In high-stakes sectors like aerospace or pharmaceuticals, a surprise hiccup can mean lost millions, so most buyers play it safe.
Finally, the green trend is changing the game. Energy efficiency, lower emissions, and smart automation are must-haves for any major purchase. German and Japanese makers especially highlight innovations that lower energy bills or boost production while keeping things eco-friendly. Some US firms now prefer “green-certified” imports over even slightly cheaper rivals if it means big power savings down the track.
- Tip: When assessing imported machinery, insist on a trial run or product demo before placing a big order. Many suppliers, even overseas ones, will schedule an online walkthrough or ship a demo unit to serious buyers.
- Tip: Keep an eye on exchange rates. The price of a Japanese or European machine can swing up or down by thousands of dollars as currencies shift. Some contracts allow buyers to lock in rates.
- Tip: If you’re a small business, don’t be shy about piggybacking on larger companies’ import channels. Join a local trade group or co-op—they often get bulk discounts.
Looking forward to the rest of 2025, the list of top US machinery suppliers is unlikely to change drastically. But technology keeps moving, and so do political winds. As American factories push further into automation, AI-driven manufacturing, and advanced health tech, expect Japan, Germany, China, Mexico, and Canada to keep duking it out at the top—each playing to their strengths, with new contenders always nipping at their heels.
Write a comment