So, you're thinking about starting a factory? Fantastic! But before you dive into this exciting venture, you'll want to know just how much cash you'll need to cover it all. The short answer? It depends. But let's break it down so you can get a clearer picture.
The first big decision is what kind of factory you're aiming to build. Whether it's food production, textiles, or electronics, each comes with its own price tag. Size matters, too—are you starting small and nimble, or thinking big from the get-go? The math is simple but crucial: bigger projects mean bigger bucks.
Now, let's talk location. It's not just about picking a place; it's about picking the right place. Real estate costs vary wildly depending on where you plant your roots. And hey, don't forget about permits and regulations. You want to make sure your dream doesn't get tangled up in red tape.
Once you've sorted the where, it's time to gear up. Equipment isn't just a one-time buy; technology upgrades and maintenance need to fit into your budget. Look out for financing options that might help spread these costs over time, making it easier to manage the cash flow.
Lastly, those sneaky ongoing expenses—wages, raw materials, utilities. They may not be upfront costs, but they'll be constant. Getting a good grip on these will help keep your factory running smoothly and in the black.
- Initial Costs and Planning
- Location and Facility Considerations
- Equipment and Technology
- Ongoing Expenses and Financial Management
Initial Costs and Planning
Kicking off a factory isn't just about having a bright idea; it's about crunching numbers and getting your ducks in a row. Your journey begins with understanding the critical initial costs that lay the groundwork for success.
Getting the Permits and Registrations Right
Before you even think about putting a shovel in the ground, you'll need to sift through an array of permits and registrations. Costs here can range anywhere from a few hundred to several thousand dollars, depending on the industry and location. This step is crucial to ensure your manufacturing operations are compliant with local laws.
Breaking Down the Budget
Here's where things get real. The budget includes costs for site preparation, construction, and essential infrastructure like water and electricity. Each of these elements has its own price variation based on your choices. Construction? That could run you anywhere from $100,000 to millions, depending on size and complexity. Infrastructure? Factor in tens of thousands more.
Equipment and Machinery
No factory is complete without robust equipment. The costs here will depend heavily on what you're planning to produce. For example, a textile factory might need weaving machines, totaling to around $500,000. While these figures might seem daunting, there are options for leasing equipment to reduce initial costs.
Staffing and Training
Even in the planning phase, it’s crucial to think about staffing. This isn't just about hiring but also training. Initial training programs are an investment, which might cost a few thousand dollars. Well-trained staff improve efficiency, so this is money well-spent.
Expense Type | Estimated Cost Range ($) |
---|---|
Permits and Registrations | 500 - 5,000 |
Construction and Infrastructure | 100,000 - 2,000,000 |
Equipment and Machinery | 200,000 - 1,000,000 |
Staffing and Training | 5,000 - 50,000 |
Mapping out these initial costs isn't just smart; it's essential. Understanding these expenses equips you with the clarity needed to seek potential financing and grants to support your business.
Location and Facility Considerations
When you're setting up a factory, picking the right spot isn't just about finding any available piece of land. There's a lot riding on location, and sometimes, it's the make or break for your whole manufacturing business.
Strategic Location
The first step is to identify a location that's not only affordable but also strategically beneficial. Ask yourself, is it close to suppliers and customers? Being near major transportation hubs like highways, ports, or railroads can save both time and money in logistics and shipping costs.
Zoning and Regulations
Different areas have different rules. Check the zoning laws to ensure your choice of location is suitable for industrial use. Missing this step could mean costly relocations or renovations. Don't overlook environmental regulations either—they affect site selection and can lead to unforeseen expenses if not adequately planned for.
Cost of Real Estate
Prices for industrial real estate can vary significantly based on the city and neighborhood. Urban areas might offer better access to skilled labor but come at a higher price. Sometimes the outskirts can offer more affordable options, but do the math on extra transportation costs. A factory needs space, but it shouldn't break the bank. Keep an eye out for industrial parks that might offer attractive deals or infrastructure support.
Utilities and Infrastructure
A manufacturing site needs robust infrastructure. This includes access to water, electricity, natural gas, and waste management facilities. Often, utility costs are ongoing expenses, so securing a location with existing infrastructure is a smart move.
Here's a useful table for utility costs across various locations:
Location | Electricity Cost (per kWh) | Water Cost (per gallon) |
---|---|---|
New York | $0.17 | $0.015 |
Texas | $0.09 | $0.010 |
California | $0.20 | $0.025 |
Expansion Potential
Think long-term. Will the site allow for expansion if your business grows? Relocating a thriving factory is hard and expensive, so it's wise to plan for growth from the start. Ensure there's room to add more production lines or storage facilities down the line.
The right location isn't just about what works today; it's about what will work in the future. Weighing these factors carefully can help position your business for success.
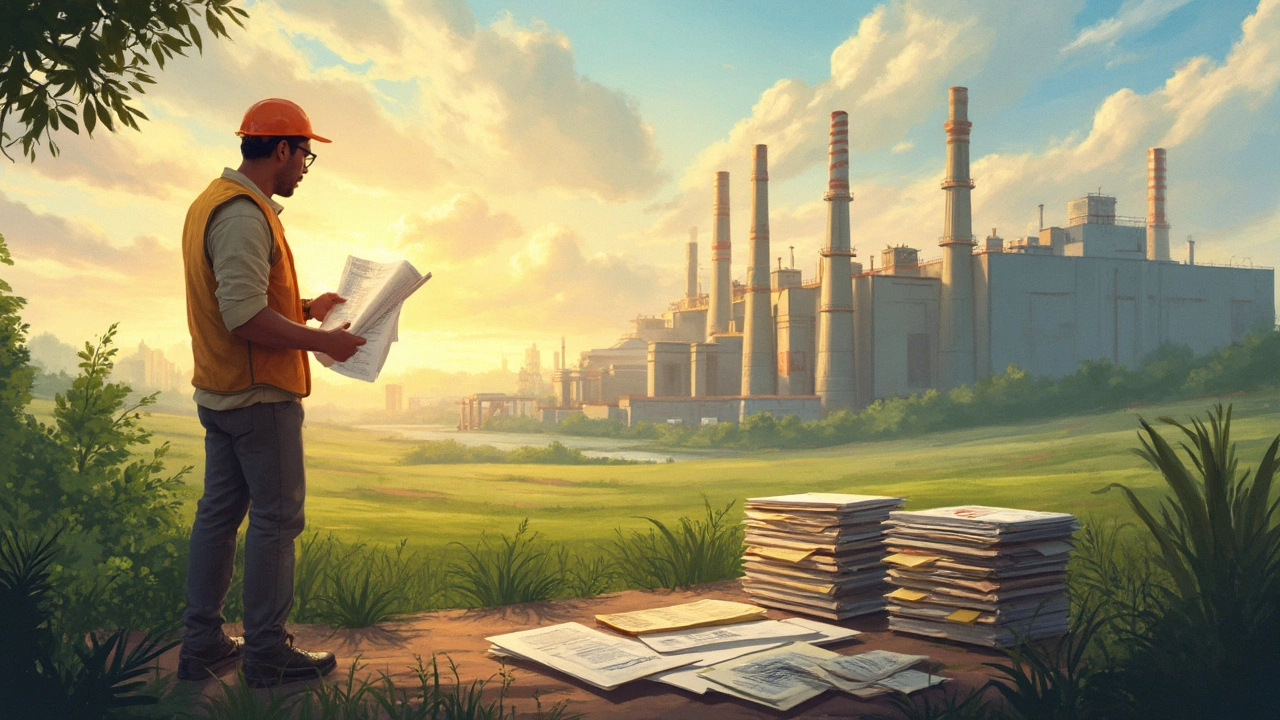
Equipment and Technology
Diving into the world of manufacturing, getting the right equipment isn't just important—it's crucial. Whether we're talking about assembly lines or specialized machinery, having the right tools can make or break your factory. But what exactly do you need, and how much is it going to set you back?
The type of factory you're planning will determine the equipment you need. For instance, a clothing manufacturer might need sewing machines and cutting tables, while a food processing plant might require mixers and sterilizers. Each industry has its own set of machinery, and it's imperative to know your needs inside out.
"Investing in state-of-the-art technology upfront can offer significant long-term savings and efficiency improvements." - John Smith, Industrial Equipment Specialist
The Cost Factor
Let's talk numbers. Depending on the size and industry, basic machinery can cost from a few thousand dollars to several figures. Big ticket items like CNC machines or robotics can go into hundreds of thousands. Look for used or refurbished options if you're tight on cash—you might score high-quality machines at a fraction of the price.
Staying Modern
Technology is always evolving. You might start with a baseline set of equipment, but expect to upgrade or expand down the line. Keep an eye on industry trends for tech that increases productivity or quality. It's often worth the investment upfront to save money and headaches later.
- Automation: Automating simple tasks can save labor costs and time.
- Maintenance: Factor regular maintenance into your budget to prevent costly breakdowns.
- Training: New tech often requires new skills; allocate resources for employee training.
Also, consider leasing instead of buying. Leasing tech equipment allows you to upgrade more easily and keep up with the latest advancements without a huge upfront investment.
To wrap it up, get what suits your needs now but have an eye on the future. Balance between cost and efficiency can totally set the stage for your success in the manufacturing world.
Ongoing Expenses and Financial Management
Alright, so you've set up your factory and got it all ready to roll. But, wait—you have to keep it running! Here, we'll break down what you'll need to keep in mind when it comes to ongoing expenses and how to handle your factory's finances smartly.
Payroll and Labor Costs
First, there's the people side of things. Your workforce will be a major part of your expenses. Salaries, benefits, and even overtime pay can add up fast. You might want to consider investing in automation where possible, but remember that skilled labor is crucial, too. A solid payroll plan helps you budget better and avoid any nasty surprises.
Raw Materials and Supplies
Now, let's talk raw materials. Prices can be unpredictable—they might shift with market changes or global events. A good practice is to establish relationships with multiple suppliers. That way, you've got options, and you can choose the best deal without compromising on quality.
Utilities and Maintenance
These might not be flashy costs, but they're important. Water, electricity, and waste management can take a hefty chunk of your budget if not monitored. Aiming for energy efficiency helps cut down on utility bills. Also, don't skimp on maintenance; regular checks prevent breakdowns and expensive repairs.
Insurance and Compliance
Peace of mind isn't free, but it's worth it. Insurance protects your assets and employees, which is crucial. Keeping up with industry regulations and compliance requirements also ensures you avoid fines and legal issues. Keeping a tight ship here means less to worry about in the long run.
Smart Financial Management
Managing your money is all about ensuring steady cash flow. Consider these tips:
- Create a detailed budget and review it regularly.
- Use accounting software to track expenses in real-time.
- Be mindful of debt and manage credit wisely.
- Set aside an emergency fund for unexpected bumps in the road.
And if numbers aren't your thing, don’t hesitate to bring in a financial advisor. It's an expense, but a good one at that. They can help you spot trends, cut unnecessary costs, and maximize profits.
Remember, staying on top of these ongoing expenses will not only keep your factory operational but also profitable. And, that’s the goal, right?
Write a comment