In the dynamic world of food processing, new terms and technologies often emerge to improve the way we handle our food. One such term you might have come across is DPU, which plays an intriguing role in the industry. If you're knee-deep in the food sector, or simply an enthusiast trying to understand how the magic happens in processing plants, this article will guide you through the essentials of what a DPU entails.
DPUs, known as Decentralized Processing Units, are reshaping how food processing systems operate by enhancing efficiency and quality control. From minimizing waste to ensuring uniform processing, these units offer a host of benefits that are critical in today's fast-paced industry. Dive in to discover how DPUs can streamline production lines and what the future holds for this innovative approach.
- What is a DPU?
- Role of DPU in Food Processing
- Benefits of Using DPUs
- Challenges Faced by DPUs
- Future of DPUs in the Industry
- Practical Tips for Implementing DPUs
What is a DPU?
Deep in the heart of food processing, the term DPU stands as a guardian of efficiency and quality. But what exactly does DPU mean? DPU denotes a Decentralized Processing Unit, a dynamic component within the food processing world. As industries seek to streamline operations, reduce bottlenecks, and enhance productivity, DPUs have increasingly come to the forefront. These units operate as independent processors within a larger system, handling specific tasks and contributing to the overarching goal of efficiency. It's like having a multitude of mini-processing factories working under the same roof, yet independently managing various facets of the production process.
The concept of decentralization in processing isn't new but applying it meticulously in the food sector is gaining momentum. By allowing individual units to handle distinct roles, the agility and speed of production lines can improve significantly. Think of a DPU as an essential cog in the grand machinery, each with its specialized task ensuring the seamless transition from raw ingredient to finished product. This modular approach not only empowers food processing facilities to be versatile but also helps them adapt to changing demands swiftly without overhauling entire systems.
Industry experts often praise the practical benefits of DPUs. They highlight their ability to reduce the downtime associated with centralized systems, a critical factor when dealing with perishable goods. By decentralizing processes, facilities can maintain continuous operation, rapidly addressing and isolating issues without bringing everything to a halt. According to Charles Hammond, a noted analyst in food technology, "The decentralized approach offered by DPUs offers a revolutionary shift in how we think of processing, offering not just efficiency but resilience against systemic failures."
More importantly, the technology behind DPUs allows for remarkable customization. Whether it is sorting, packaging, or processing, each unit can be tailored to fit the needs of a specific task. This customization is vital when dealing with specialty products and diverse consumer demands. Facilities can maintain strict quality control over each stage, ensuring that the end product consistently meets established standards. It's no wonder why DPUs are steadily becoming the backbone of modern food processing infrastructure worldwide.
In terms of data and monitoring, DPUs also provide a strategic advantage. With each unit capable of handling real-time data, operators gain granular insight into each step of the processing line. This insight aids in identifying inefficiencies, forecasting maintenance needs, and optimizing schedules. It creates an environment where proactive management rather than reactive responses becomes the norm, leading to better resource allocation and less waste. The result is not only cost savings but an eco-friendly approach to food production that aligns with contemporary industry goals.
Reflecting on the technology's adoption, we can also consider its global reach. Advances in DPU technology have not only benefitted large-scale food processors but also empowered smaller, decentralized facilities. This democratization of processing technology allows for localized food production, reducing transportation costs and supporting regional economies. An example can be drawn from New Zealand, where the agility provided by DPUs has supported its dairy industry's expansion into new markets without compromising quality or sustainability.
Role of DPU in Food Processing
Understanding the role of DPU in the food processing industry is crucial for grasping how modern technology enhances operational efficiency. A Decentralized Processing Unit, or DPU, serves as an essential component in the evolution of food processing. Unlike centralized systems where processing is confined to one location, DPUs allow for the distribution of processing tasks across different units. This means that each unit in the network can manage and process food independently, vastly improving not only the speed of operations but also reducing the potential for bottlenecks in production.
For instance, in a sprawling food production facility churning out tons of cereal daily, having a DPU means that each unit can handle specific tasks like mixing, heating, or packaging independently. This decentralization reduces downtime and increases output. Also, with today's focus on sustainability, DPUs contribute significantly by lending flexibility to production schedules. Factories can easily switch to different products without a significant overhaul, saving time and resources. Such adaptability feeds into the continuous demand changes seen in the market, where consumer preferences can shift swiftly.
Many industry insiders speak highly of DPUs due to their contribution to streamlined operations. According to an expert from the International Food Processing Association,
"Decentralized Processing Units have revolutionized the way food is processed, offering industries the potential for not only efficiency but innovation in food safety and quality."This quote underscores the profound impact that efficiency in food processing has on other aspects like food safety, a topic that never goes amiss in today’s health-conscious society.
The introduction of DPUs goes beyond operation enhancements. They bring about a noticeable improvement in energy consumption. Since tasks are distributed, each DPU can power down when not in use, conserving energy. This ability to optimize power usage without impacting productivity makes DPUs a sustainable choice, aligning with worldwide calls for reduced energy footprints in industrial sectors. However, it's worth mentioning that deploying DPUs comes with its share of challenges. These include higher setup costs and complex logistics involved in syncing multiple units effectively.
Nevertheless, many believe these challenges can be managed or mitigated with proper planning and investment in skilled personnel. In the broader picture, as the food industry embraces more DPU installations, it's anticipated that these units will become even more efficient and user-friendly. With advancements in AI and machine learning, DPUs are expected to gain smarter capabilities, predicting maintenance needs before a breakdown happens, thereby decreasing unplanned downtimes even further.
Strategically, companies keen on utilizing DPUs must ensure thorough training for their staff. Operators need to be comfortable and adept with the technology that powers these units. This investment into human capital is as significant as the capital expenditure on the units themselves. Aligning both human expertise with technological advancements is key to leveraging the full potential that DPUs offer in the food processing realm.
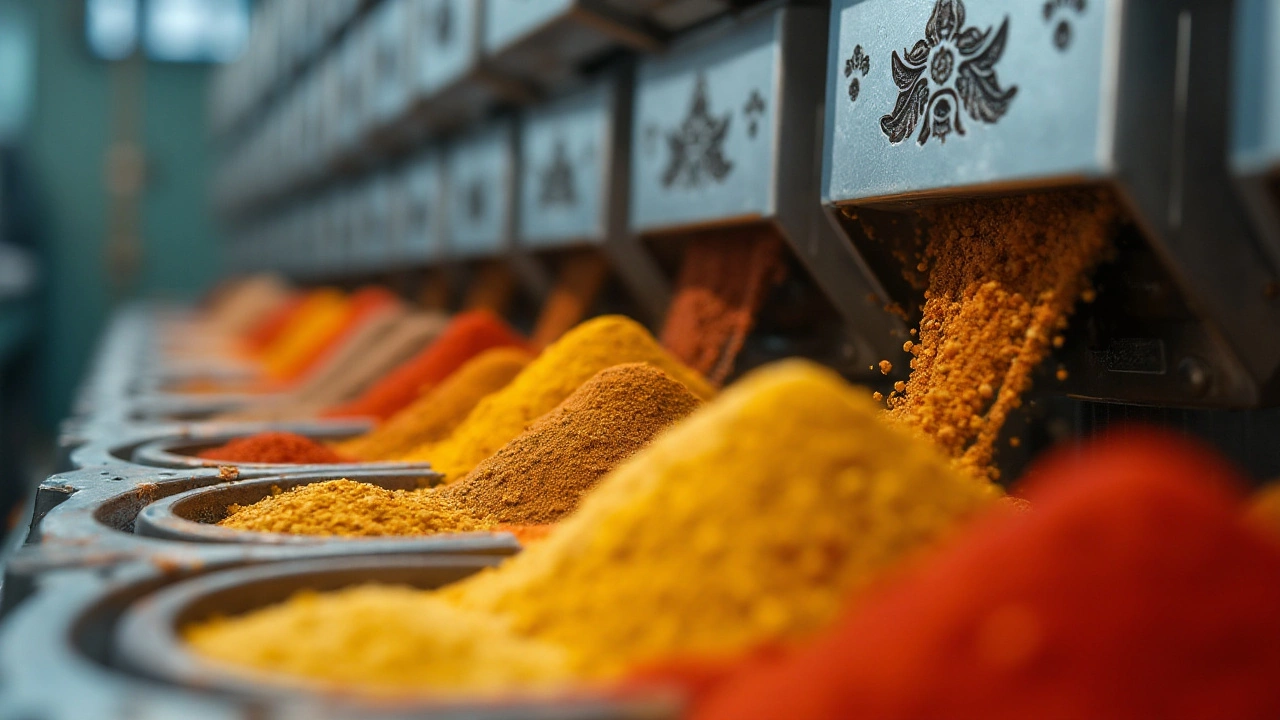
Benefits of Using DPUs
The use of DPUs in the food processing industry is transforming production methods, which is evident in the sweeping changes across diverse food sectors. First and foremost, one of the significant advantages is the boost in efficiency. Traditional centralized processing systems can face bottlenecks due to high demand or varied product lines, leading to delays and potential revenue loss. In contrast, DPUs can operate independently, strategically decentralizing the workload across multiple units, hence streamlining the entire process. This decentralization allows for different product types to be processed simultaneously without interference or downtime, thereby enhancing the overall production speed.
Moreover, quality control is another major advantage when integrating DPUs. With the ability to focus processing efforts on smaller batches, DPU systems can ensure more consistent monitoring of each stage, from raw material intake to the final output. Enhanced scrutiny at each processing step means fewer errors and deviations, leading to a higher quality end product. By maintaining strict quality checks, companies can build customer trust and ensure compliance with food safety standards. According to a recent industry report, companies employing DPUs reported a significant reduction in waste materials, attributing this improvement to precise control and monitoring capabilities.
Adapting to market trends and consumer demands is another key benefit. The food industry is notorious for its rapidly shifting consumer preferences, driven by new dietary trends and health consciousness. DPUs offer the agility needed to pivot operations and innovate with new product lines without major overhauls to existing setups. This adaptability is crucial in staying competitive and meeting the diverse needs of today's consumers. The capability to quickly implement adjustments in processing parameters facilitates experimentation with flavors, textures, and nutritional content, which may not be as feasible with traditional centralized systems.
There are environmental benefits associated with utilizing DPUs. These systems typically consume less energy compared to larger, older centralized processing plants, contributing to a reduction in carbon emissions. By optimizing energy use tailored to specific tasks rather than an entire line, companies can significantly lower their ecological footprint. Such a commitment to sustainable practices not only helps the planet but also enhances a company's reputation among eco-conscious consumers. According to a survey conducted by the Food Processors' Association, nearly 68% of companies with DPUs reported an improvement in their sustainability ratings.
"The adoption of decentralized processing units is not just a technological upgrade but a strategic shift towards efficiency, quality, and sustainability," noted Dr. Oliver Green, a leading expert in food technologies.
Lastly, employing DPUs can offer substantial cost savings. The initial investment might seem daunting, but the long-term benefits are undeniable. Reduced waste, improved energy efficiency, and lower maintenance costs due to smaller, more manageable units result in considerable financial advantages. Companies can see enhanced profit margins, allowing them to reinvest in other growth areas such as research and development or marketing strategies, further securing their position in the competitive market.
Challenges Faced by DPUs
Decentralized Processing Units, while promising advanced efficiency in food processing, bring an array of challenges that industry players must navigate. Firstly, the integration of DPUs into existing systems is a hefty task, often requiring a complete overhaul of infrastructure. This process not only demands a significant investment of time and financial resources but also involves potential downtime during the transition period, which could disrupt ongoing operations. Companies must weigh the cost of this integration against potential long-term savings and improvements in productivity.
Another significant hurdle is the requirement for specialized skills to operate and maintain these units. The complexity of DPUs demands expertise that might not be readily available within traditional processing teams. As a result, businesses often need to invest in specialized training programs or hire skilled professionals, which can be resource-intensive. This need for specialized knowledge extends beyond mere operation; maintenance of DPUs also requires advanced technical acumen to troubleshoot and rectify the unique issues that these units may present.
Moreover, compatibility with existing technology systems poses a notable challenge. DPUs must seamlessly connect and communicate with other parts of the food processing line, which often run on varied and incompatible technologies. Achieving this interoperability can be complex, potentially necessitating custom-built software solutions or intermediary systems that can mediate between different technological languages. Without seamless integration, the promised efficiencies of DPUs may remain out of reach.
From a regulatory perspective, DPUs do not operate in a vacuum. They must comply with stringent food safety and industry standards. Therefore, staying abreast of ever-evolving regulations and ensuring that DPUs meet these requirements is crucial. This includes having appropriate documentation and processes in place to demonstrate compliance during inspections. Failure to meet these standards could lead to significant financial and reputational consequences.
The rapid pace of technological advancement is another factor that cannot be ignored. As new innovations continuously emerge, even the most advanced DPUs can quickly become obsolete. This necessitates a forward-thinking approach to investment and scaling up operations, ensuring that DPUs remain adaptable and capable of integrating future technologies. Companies must strike a delicate balance between upgrading existing systems and adopting developing technologies.
Lastly, while DPUs promise significant benefits in terms of reducing energy consumption, they also introduce new environmental challenges. The materials used in their construction and ongoing energy requirements may contribute to a larger carbon footprint if not managed properly. Companies must be proactive in sourcing sustainable materials and optimizing the energy efficiency of these units to truly benefit from a reduced environmental impact. Reports suggest that "innovation is crucial to maintaining competitive advantage and ensuring sustainability in operations," highlighting the importance of embracing and overcoming these challenges.
"The key to successful DPU integration lies in a strategic approach to innovation, allowing companies to rise above technological and operational hurdles," says industry expert John Mitchell.
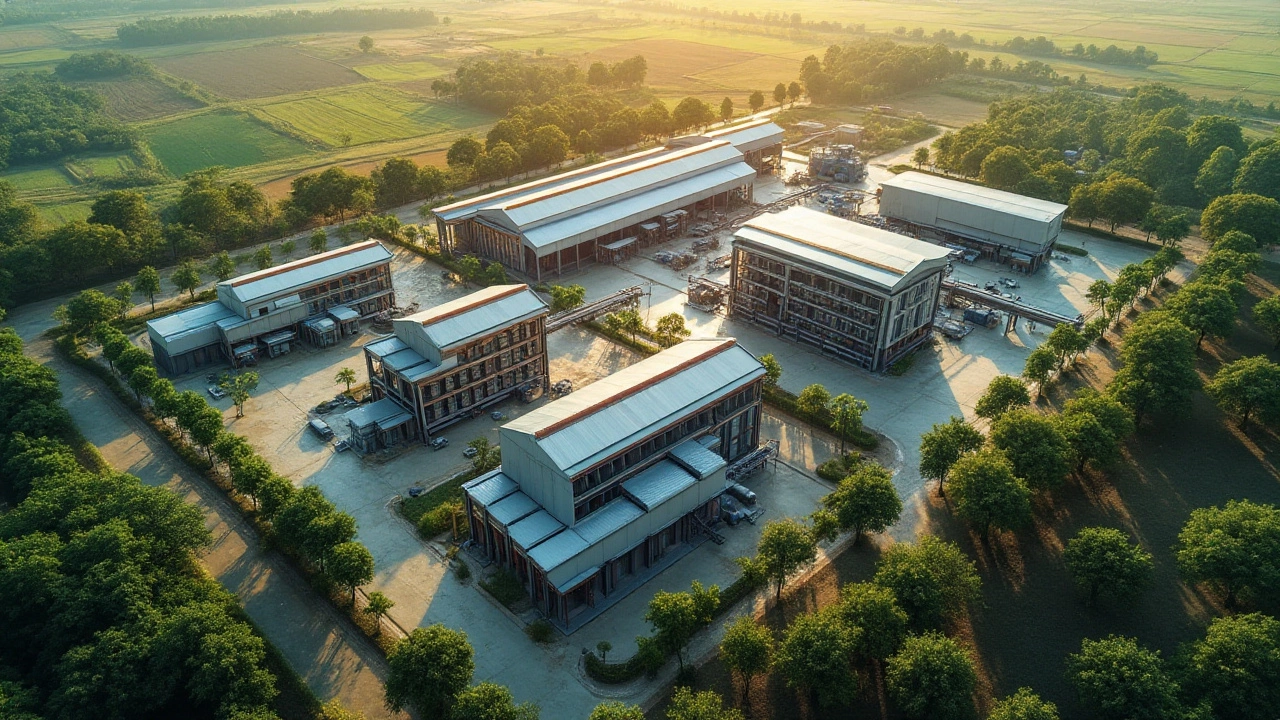
Future of DPUs in the Industry
The future of DPUs in the food processing industry looks more promising than ever. As the world demands more efficient and sustainable ways to process food, these units are poised to play a significant role in transforming operations. Imagine walking into a facility where each section optimally functions through a network of small yet powerful processing units, all fine-tuning the production process in real-time. This isn't just a dream; it's a reality within reach, thanks to the ongoing advancements in DPU technology.
One reason why DPUs are gaining traction is their ability to adapt to rapidly changing consumer preferences. The modern buyer seeks fresh, minimally processed foods, and DPUs offer the flexibility needed for smaller batch processing. As technology evolves, so does the capability of these decentralized units to work with a wide variety of food items. In a recent study by the Food Processing Association, 70% of surveyed plants anticipated adopting DPU systems within the next five years.
Integration with Smart Technologies
Another exciting prospect for DPUs is their integration with smart technologies, including IoT devices and advanced AI analytics. These technologies enhance their operational efficiency by constantly monitoring production variables like temperature, pressure, and ingredient composition. They provide critical data that can help fine-tune processes to reduce waste and increase output quality. This synergy between DPUs and smart tech means a future where food processing is not only more efficient but also more environmentally friendly."DPUs are paving the way for more decentralized processing models. By distributing workload across smarter units, businesses can achieve a level of agility previously unimaginable." - Dr. Lydia Chen, Industrial Process Engineer
The industry is also looking at how DPUs can aid in resource conservation. With growing concern for energy consumption and environmental impact, DPUs can be engineered to operate at optimal energy levels, reducing the carbon footprint of food processing facilities. Some experts forecast a 25% reduction in energy usage with the extensive adaptation of DPUs, which not only helps the planet but cuts costs for businesses too.
Future Challenges and Opportunities
Of course, the future isn't without its challenges. Implementing DPUs requires significant upfront investment and a shift in infrastructure. Smaller or traditional companies may struggle with these changes. Still, the long-term savings and efficiencies often outweigh the initial costs. As more success stories emerge, there's likely to be an industry shift towards embracing DPUs more wholeheartedly. Emphasizing education and training will be crucial to navigate these challenges, ensuring staff are equipped to handle the transition.- Enhanced efficiency through customized solutions
- Integration with sustainable practices
- A stepping stone toward digital transformation in the food processing industry
In summary, the future of DPUs is intertwined with the broader digital and sustainable transformation within the food industry. As these units continue to advance, they offer a route to a more efficient, agile, and eco-friendly future, maintaining their vital role in the sector. The question is not if, but when will producers fully integrate these innovative solutions into their operations. And as we ponder on this, it becomes clear that DPUs are more than just components; they are the vanguard of the next revolution in food processing.
Practical Tips for Implementing DPUs
Implementing DPUs in food processing can significantly boost your operational efficiency, but it's not just about adopting the latest tech. You must strategize to maximize the benefits. Begin by assessing your current setup and understand where DPUs could fit most effectively. It's essential to map out your operational flow to identify bottlenecks that these units can address. Engaging with stakeholders, from technicians to management, early in the process ensures a smooth transition and wide acceptance of changes. Clear communication about what DPUs are, their role, and benefits is crucial to gaining buy-in from your team.
Once you've got everyone on board, the next step is a detailed analysis of the food processing cycle within your business. Evaluate which stages are critical and require the increased precision that DPUs can provide. Some plants have reported up to 20% improvement in yield after implementing these units. Consider organizing workshops or training sessions to familiarize your staff with new processes. Training should cover not only the use of DPUs but also maintenance practices to avoid downtimes and disruptions. A trained team can significantly cut costs associated with machinery breakdowns and ensure continuous operation.
Investing in technology is vital, but it's just as vital to have a robust maintenance schedule. Regular checks and timely updates keep your DPUs in peak condition, which is crucial for maintaining product quality. Consider establishing a dedicated team for this task. They should be equipped with specific diagnostic tools and spare parts, reducing the response time to any issues. If new to DPUs, you might engage with technology partners who offer insights and professional support during the initial phases. Some companies report that third-party experts have helped reduce inefficiencies by up to 30% during the first year.
"Innovation distinguishes between a leader and a follower." - Steve Jobs
As you move forward, keep an eye on industry trends and technological advancements. Food processing is a rapidly evolving field, and staying updated will entice you towards potential upgrades or modifications to your existing DPU systems. Attending industry expos and seminars can provide insights and offer networking opportunities with others who have successfully integrated DPUs. This proactive approach helps you not only in keeping the system current but also in outpacing competition with innovative solutions.
Finally, measure success through a series of key performance indicators (KPIs). These could include efficiency rates, product consistency, and waste reduction metrics. Regularly reviewing these KPIs helps in understanding the impact of DPUs on your operations and any adjustments needed. A dedication to continuous improvement through regular reviews ensures you get the most out of your investment, creating a robust and future-proof processing environment.
Write a comment