Ever wondered just how many steel plants actually run in the US right now? If you search online, the numbers can get pretty confusing—some sources throw in little foundries, others only count big blast furnaces, and a few just toss out old data. Straight up: as of June 2025, there are right around 90 major steel plants scattered across the country, give or take a few. This count doesn't just include the giants rolling out thick slabs of steel. It also covers smaller specialty mills rolling out those custom alloys used in everything from cars to skyscrapers.
Most people picture these plants towering over old industrial towns, but they’re not just throwbacks to the past. Today’s facilities are high-tech and run more efficiently than ever. They’re tucked away near rail lines, highways, and even rivers to keep shipping smooth and costs down. So, whether you’re mapping out supply chains or just want to know what’s fueling modern construction, these plants play a bigger role in day-to-day life than you might think.
- What Counts as a Steel Plant?
- The Current Number: Real Data from 2025
- Where Are They Located?
- Who Runs the Big Plants?
- What’s Changing in American Steel?
What Counts as a Steel Plant?
This question trips up a lot of people. Not every place with a smokestack and a pile of scrap metal counts as a steel plant. In the US, a real steel plant is a facility that takes raw materials—like iron ore or scrap—and turns them into finished steel by melting, refining, and shaping. Plants that only cut, coat, or bend steel from somewhere else don’t make the list here.
There are two main types of plants that go into the official count:
- Integrated mills: These are the classic giants. They start with raw iron ore, cook it in blast furnaces, and churn out everything from steel slabs to coils. Think U.S. Steel or Cleveland-Cliffs facilities. They handle every step and use tons of energy but can make huge volumes at once.
- Mini-mills (or EAFs): These are way more common now. Instead of starting with iron ore, they use electric arc furnaces (EAFs) to melt down scrap steel or sometimes even pig iron. Nucor and Steel Dynamics are the big names here. Mini-mills are usually smaller, faster, and more flexible—it’s why they’ve caught on so much.
Here’s a quick breakdown to help you spot the difference:
Type | Main Input | Main Equipment | Share of US Production (2024) |
---|---|---|---|
Integrated | Iron ore, coal | Blast furnace | 27% |
Mini-mill (EAF) | Scrap steel, pig iron | Electric arc furnace | 73% |
Here’s the catch: Foundries, steel processors, and finishing shops don’t count unless they actually make steel from scratch. You’re looking for places that either blast, melt, or arc their way from raw stuff to solid steel products. If you’re hunting for a map or a list, keep your eye on true steelmaking facilities—the backbone of the steel plants US scene.
The Current Number: Real Data from 2025
If you're looking for a straight answer on how many steel plants are running in the US right now, here it is: as of June 2025, there are 89 primary steel manufacturing plants in operation. These numbers come straight from the American Iron and Steel Institute’s latest report and they only count fully operating plants—not idled ones or facilities just making ferroalloys.
When most people talk about 'steel plants,' they're usually thinking about integrated mills with blast furnaces, or electric arc furnace (EAF) mini-mills. Both types are core parts of American steel production, but they've got different roles. Integrated mills work from iron ore and use traditional blast furnaces. Mini-mills, on the other hand, mostly recycle scrap steel.
Check out how the plant landscape really looks in 2025:
Type | Number of Plants | Main Products |
---|---|---|
Integrated Mills | 10 | Flat-rolled steel, plates, large structural steel |
Electric Arc Furnace (Mini-mills) | 79 | Rebar, wire rod, beams, sheet steel |
That’s a big shift from just a couple decades ago, when integrated mills made up a much larger part of the industry. But these days, EAF plants are spreading fast—they’ve got lower costs, use less energy, and are easier to drop closer to end users.
So, if you care about the steel plants US count for supply, jobs, or even a school project, remember that nearly nine out of every ten steel facilities in the US today are EAF mini-mills. And here’s a tip: If you’re following changes in the industry, pay attention to new EAF startups or planned closures—those swings can rejig the total number in a hurry.
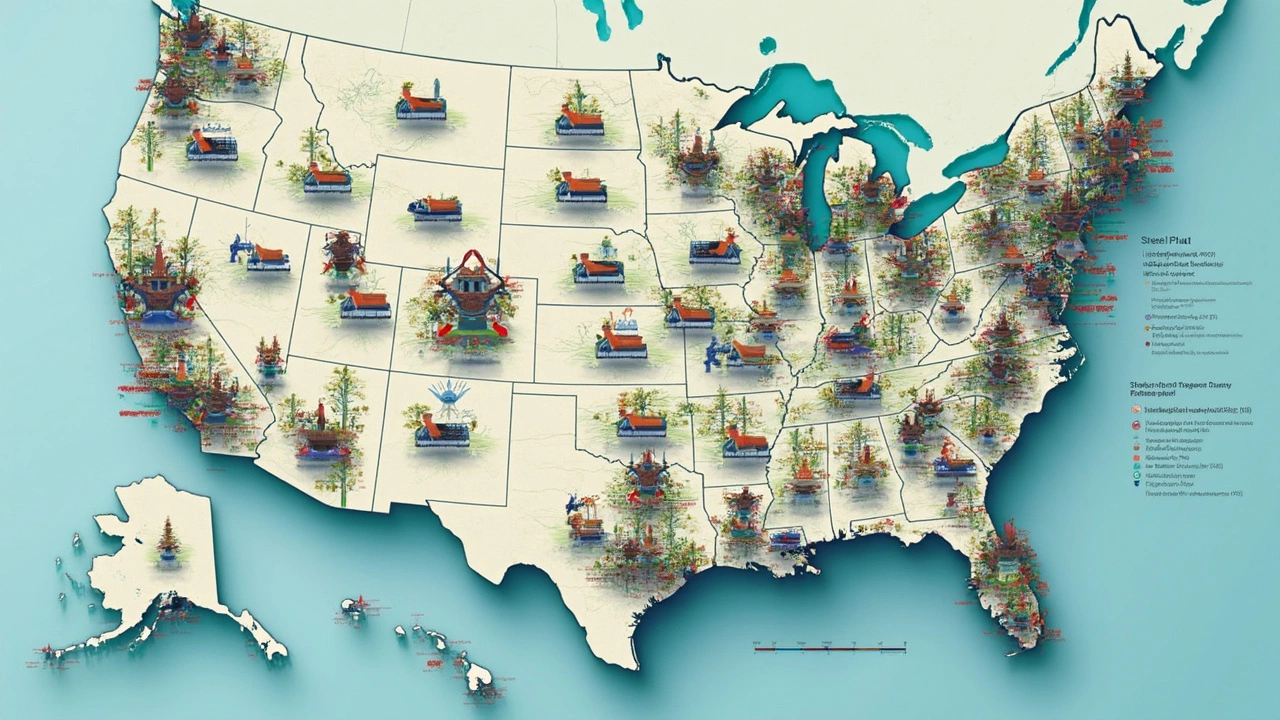
Where Are They Located?
The US steel plants aren’t just lumped together in one region—they’re really spread out, but certain spots are still the heavy hitters. The steel plants US keyword gets a lot of search traffic thanks to these established clusters everyone’s curious about. If you look across the states, most steel action happens in the Great Lakes region. Cities in Ohio, Indiana, Pennsylvania, and Illinois are still considered the backbone of American steel. Chicago and Gary are not just on the map—they’re key players, cranking out millions of tons every year.
That said, you’ll also spot big steel facilities near the Gulf Coast, in places like Texas and Alabama, mostly since it’s easier to ship raw materials there from all over the world. Mini-mills have popped up in the South because the power and labor costs are usually lower and demand for construction steel is hot in fast-growing cities.
Here’s a quick view of where the major steel plants are found by state:
State | Number of Major Plants (2025) | Key Cities |
---|---|---|
Indiana | 15 | Gary, Burns Harbor, East Chicago |
Ohio | 11 | Cleveland, Middletown, Warren |
Pennsylvania | 10 | Pittsburgh, Coatesville, Conshohocken |
Texas | 8 | Houston, Baytown, Seguin |
Alabama | 7 | Birmingham, Mobile, Tuscaloosa |
Illinois | 6 | Granite City, Joliet, Chicago |
Notice that even states with just a handful of plants (like Alabama or Texas) have some of the largest or most modern facilities running. If you’re in Michigan, Minnesota, or Arkansas, steel still makes noise there too, but on a smaller scale. And with newer mini-mills, you sometimes find steel being made in spots you wouldn’t expect—think rural Arkansas or suburban South Carolina.
If you need to check if there’s a steel plant near you or scope out where the next one might show up, keep an eye on the expanding Sunbelt region. Growth and investment are definitely shifting south, especially as companies hunt for cheaper land and easier logistics.
Who Runs the Big Plants?
If you’re looking for the biggest names behind steel plants US, think of companies like Cleveland-Cliffs, U.S. Steel, and Nucor. These guys aren’t just big—they’re giants. Together, they produce more than half the steel made in America every year.
Cleveland-Cliffs, based out of Ohio, has taken over a bunch of old legacy mills, including giants in the Midwest. In fact, by 2025, Cleveland-Cliffs alone controls more than 25% of the nation’s flat-rolled steel output. U.S. Steel, with its roots stretching back over a century, still runs huge plants like the Gary Works in Indiana, which is one of the largest in the country. Nucor does things a little differently. Instead of those old-school massive blast furnaces, Nucor mostly uses electric arc furnaces—cheaper, cleaner, and quicker to fire up. That’s helped them pop up with smaller mills all across the South and Midwest.
If you want the numbers:
Company | Headquarters | Main Production Method | # of Major US Plants | 2024 Output (million tons) |
---|---|---|---|---|
Cleveland-Cliffs | Ohio | Blast/Basic Oxygen Furnace | 10 | 17.0 |
U.S. Steel | Pennsylvania | Blast/Basic Oxygen Furnace | 5 | 11.2 |
Nucor | North Carolina | Electric Arc Furnace | 25 | 20.2 |
The rest of the industry is split between a few other players—Steel Dynamics, Gerdau, Commercial Metals Company—all with their own mix of traditional and modern plants.
All these companies tweak their operations based on what the market wants. For instance, when automakers need high-strength steel, production lines get retooled. It’s fast-paced, and nobody can just cruise on reputation.
"Our industry doesn’t sit still," says Mark Millett, CEO of Steel Dynamics. "If we’re not investing in efficiency and new products, we’re falling behind and that’s just not an option."
So, if you hear about a whopping new investment in some small town, chances are one of these names is behind it. Their decisions don’t just shape steel—they shape jobs, infrastructure, and even the price tag on your next car or washing machine.
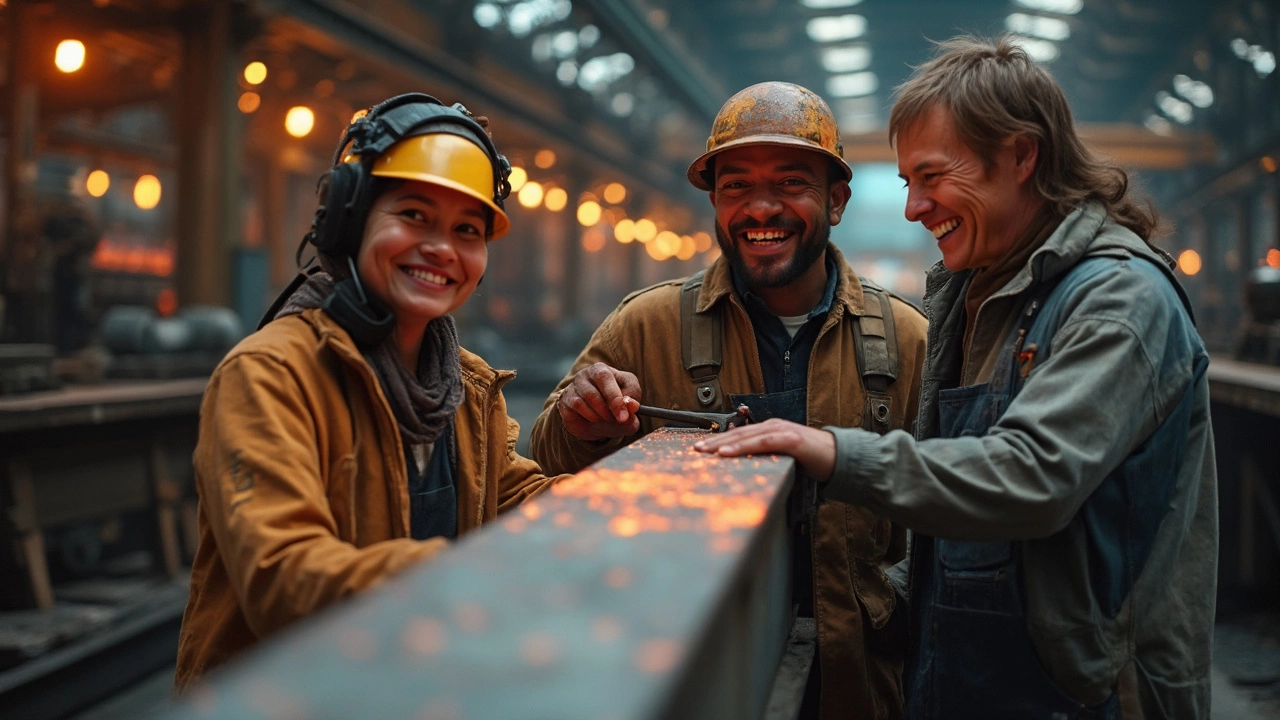
What’s Changing in American Steel?
The last few years have been wild for the American steel industry. You wouldn't recognize some of these plants compared to how they looked just a decade ago. The old image of smoke stacks and endless noise? That’s on its way out, thanks to new technology and pressure to clean up the environment.
Right now, almost every major company is racing to upgrade their equipment. We're seeing electric arc furnace (EAF) plants pop up fast. Unlike traditional blast furnaces, EAFs can melt scrap steel with electricity, cutting emissions and using way less energy. Back in 2020, EAFs made up about 70% of US steel output according to the American Iron and Steel Institute, and now it's even higher—pushing closer to 75% in 2025. That shift is huge for both jobs and pollution in factory towns.
Another big change? Automation. Robots and AI are showing up on the plant floor, which means fewer dangerous jobs but also the chance for better safety and higher skill positions. Some training centers have opened near major mills to help workers keep up. If you’re thinking about a career around steel, learning some robotics could really pay off.
Trade is also shaking things up. Old tariffs and new deals have big ripple effects. For example, in 2023, several US steel plants expanded or reopened after a wave of new infrastructure spending boosted demand. Builders need strong, affordable steel for bridges, rail, and new power grids, so plants in places like Ohio and Alabama jumped back into action.
If you plan to visit or work near a steel plants US facility, expect a site that looks more like a high-tech lab than an old factory. Safety rules are stricter, air is much cleaner, and the work is all about efficiency. The bottom line: the US steel scene is getting smarter, cleaner, and quicker every year—but you’ve got to keep an eye on these changes if you want to stay ahead.
Write a comment