Ask anyone in the game—choosing the right way to make your stuff can make or break your whole business. Here’s the thing: manufacturing isn’t a one-size-fits-all deal. Each way of making products has its own sweet spot, pain points, and startup needs. Whether you’re eyeing one-off custom gear or plan to pump out millions of units, knowing your options will save you tons of headaches (and cash down the line).
Let’s kick things off with the basics: there are five main types of manufacturing. Each one has its own set of strengths, and they’re not just for big corporations. Many smaller businesses are using leaner, smarter versions of these models to gain an edge. It’s all about picking the one that fits your product, your market, and your budget.
- Job Shop: Custom Orders, High Flexibility
- Batch Production: Best for Small to Mid-Sized Runs
- Assembly Line: Mass Production Made Simple
- Continuous Flow & Lean Manufacturing: Maximum Efficiency
Job Shop: Custom Orders, High Flexibility
If you’re talking about manufacturing types that thrive on variety and custom work, job shop is at the top of the list. It’s the go-to choice for businesses that make specialized products or small batches with tons of variation. Think machine shops, custom furniture builders, or even some small-batch clothing brands.
In a job shop, the setup is all about flexibility. Instead of long rows of machines built for a single product, you’ve got workstations or machines that switch between different jobs. Each project is almost like its own adventure—one week you’re building custom bike frames, the next you’re making replacement parts for vintage cars.
One big perk: If your customer wants a one-off design or unusual materials, you can say yes. That means you can charge more, since mass producers can’t touch this level of customization. According to the U.S. Small Business Administration, job shops are “uniquely positioned to serve markets that larger manufacturers can’t easily access due to volume or specialization constraints.”
“Job shop manufacturing is the backbone of small and medium-sized business innovation. It’s where unique ideas turn into real products, one order at a time.”
— Manufacturing USA Network
Here’s the catch—because every order is different, you need skilled workers and tight organization. Your lead times might be longer, and costs can be unpredictable if you don’t track things closely.
- Best for: Custom parts, prototypes, products with lots of variety
- Must-have: Flexible equipment, skilled team, customizable workflows
- Potential downsides: Higher costs, tough to scale, scheduling headaches
If you’re just starting out or focusing on a manufacturing business where every order is different, job shop gives you more control. It lets you take advantage of niche markets where customers want something better than cookie-cutter. Just be ready for complexity—your success depends on managing all those moving parts without missing a beat.
Batch Production: Best for Small to Mid-Sized Runs
Batch production really shines for companies that don’t need to churn out massive volumes but also want more than just one-off products. This method means you manufacture products in groups or “batches,” moving them through each stage of production together. If you’ve ever noticed how bakeries bake dozens of loaves at a time—rather than one after another—you’ve seen batch production in action.
Why choose this manufacturing type? Flexibility is a big reason. You can make batches of different products without having to change your whole setup. For example, a small clothing brand might sew 200 red T-shirts and then quickly switch to 200 in blue. This keeps things manageable and helps control costs since you’re not committed to massive runs or setups.
Here are a few places where batch production is a go-to:
- Bakeries, breweries, and food producers—think cookies, bottled drinks, or frozen meals.
- Cosmetics and skincare—batches of lotions or hair products.
- Small electronics—like specialty speakers or certain medical devices.
Managing batch production does require some planning. You need to track inventory closely and plan your batches so you don’t run out of supplies or end up with too much unsold stock. A batch’s size has to fit your sales demand—make too many and you might end up with waste; too few, and you could lose sales.
The tech side matters too. With basic equipment and a little automation, you can usually get started without breaking the bank. Plus, many modern batch producers now use software to track everything, from ingredients to delivery schedules, making it way easier to stay organized and keep customers happy.
Output Volume | Product Variety | Typical Setup Cost |
---|---|---|
Low to Mid | Wide | Moderate |
If you need advice on getting going, keep your first batches small while you figure out your systems, then scale up once you know what works. Also, keep in mind that quality control should happen between every batch—so you can catch problems before they pile up.
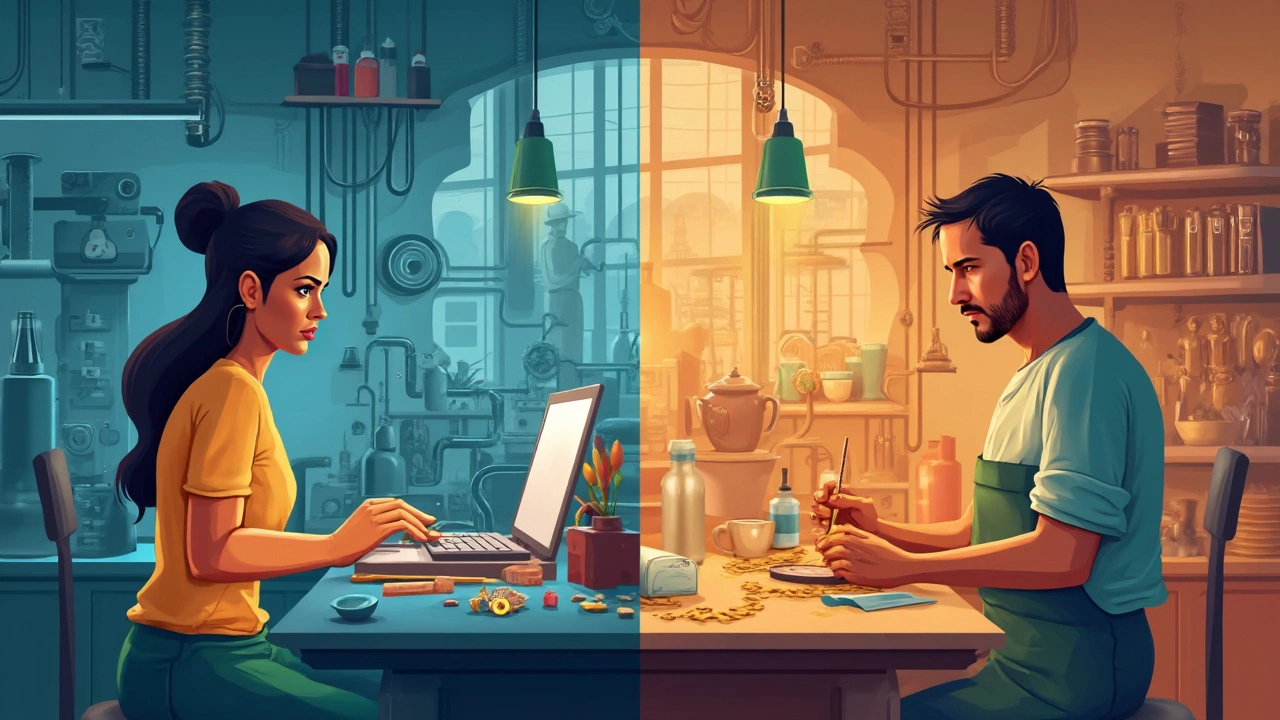
Assembly Line: Mass Production Made Simple
If you’ve watched cars roll out of a factory—or even toyed with Lego assembly sets—you already get the basic idea behind the assembly line. It’s all about mass production and doing it fast. The assembly line chops the job into steps, so each worker or robot handles just one task. The result? Loads of finished products, all looking the same, pumping out at lightning speed.
Henry Ford didn’t invent the concept, but he made it famous in 1913 at his Detroit plant. By switching to an assembly line, Ford more than doubled production and slashed the time it took to build a single Model T from over 12 hours to just 90 minutes. Since then, this method has powered everything from smartphones to sneakers.
Why is an assembly line such a game-changer for manufacturing types? Here’s the key:
- It cuts down wasted time and movement, making everything fast and efficient.
- It makes training easier. Workers or machines repeat just one or two tasks instead of learning it all.
- Bigger volume means lower cost per item—so you can compete on price.
- Everything gets standardized. Less chance for mistakes, more reliability.
Plenty of businesses use this setup, especially if you’re making thousands (or millions) of the same thing, like bottled drinks, electronics, toys, or furniture parts. But there’s a catch: high upfront costs. It takes serious investment to set up machines, design workflows, and keep things running steady. On the upside, you can pump out crazy amounts of product once you're set up.
Industry | Product | Typical Output (units/year) |
---|---|---|
Automotive | Car assembly | 8 million (Toyota, 2023) |
Electronics | Smartphones | 230 million (Apple iPhones, 2023) |
Food & Beverage | Bottled soft drinks | Billions (Coca-Cola, annual global) |
If you’re exploring manufacturing business ideas in a space where products don’t change much, and you can sell big numbers, going the assembly line route can be a ticket to scale and profit. Just don’t dive in before you’re ready to handle the volume and the setup. Sometimes, automation lets even smaller outfits play in this game thanks to cheaper robots and software. So if you think you can carve out a niche with consistency and volume, assembly lines are worth a hard look.
Continuous Flow & Lean Manufacturing: Maximum Efficiency
If you’re in the business of making stuff 24/7—think toilet paper, bottled water, or gasoline—continuous flow manufacturing is the way to go. This method is all about nonstop production. The machines rarely stop, which means products just keep rolling out. A real-world example? The chocolate bars you snag at the store. Big companies run those production lines at full speed, day and night.
This method’s superpower is efficiency. When your setup is dialed in, you’ll hit crazy-high output and keep your costs down per unit. That’s why mass production giants use it. But here’s the trade-off: you need tons of upfront cash for equipment, and you better love making the same thing over and over, because switching gears is a nightmare.
Now, on to lean manufacturing. This idea comes from Toyota and took off worldwide. The goal is simple: cut out everything that wastes time, space, or raw material. Lean is about working smarter, not harder. It’s got a few main moves:
- Organizing your workspace so nothing’s ever lost or out of reach
- Setting up systems to catch glitches before they snowball
- Producing only what’s needed to avoid piles of unsold stock
- Getting team feedback so you can improve—every day
Lean can work with almost any of the manufacturing types. A small custom shop can use lean tricks to boost output and cut downtime, while massive factories go all-in to save millions. The best part? Lean isn’t all-or-nothing. Start with one small change (like cutting travel time between tools), and build from there.
Production Method | When to Use | Biggest Strength |
---|---|---|
Continuous Flow | High volume, standard products | Max output, lowest unit cost |
Lean Manufacturing | Flexibility needed, want less waste | Reduces costs, boosts efficiency |
If you’re gunning for top efficiency or already know you’ll sell serious volume, continuous flow is unbeatable. If you want to trim fat, boost speed, and maybe even help the planet by wasting less, lean manufacturing is where to start. Either way, these two approaches can turbocharge your manufacturing business—and keep you ahead of the competition.
Write a comment